The development and distribution of vaccines have been instrumental in preventing and controlling infectious diseases worldwide.
However, vaccines’ production and quality control are subject to stringent regulatory requirements to ensure their safety, efficacy, and consistent quality.
Meeting these standards is critical to prevent adverse events and ensure the effectiveness of vaccines in protecting public health.
This article helps to understand the essentiality of the regulatory aspects for policymakers, vaccine manufacturers, and healthcare professionals to promote the availability and accessibility of safe and effective vaccines.
- Regulatory Aspects of Vaccine Manufacturing
- Role of Cleanrooms in Vaccine Manufacturing
- Understanding the GMP and cGMP Standards in Vaccine Manufacturing (KW here)
- Quality Control in Vaccine Manufacturing
- Challenges and Trends in Regulatory Aspects of Vaccine Manufacturing
- The Role of Technology in Vaccine Manufacturing
- To Wrap it Up
Regulatory Aspects of Vaccine Manufacturing

The manufacturing of vaccines is subject to rigorous regulatory oversight to ensure that they meet the required standards for safety, efficacy, and quality.
The regulatory aspects of vaccine manufacturing involve compliance with international guidelines and regulations, like those set by the World Health Organization (WHO) and authorities in different countries.
The manufacturing process for vaccines typically involves several stages. It includes the cultivation of the microorganisms or cells used to produce the vaccine, purification, and formulation of the final product, and testing for safety, potency, and quality.
In addition, each stage must adhere to strict regulatory requirements to ensure the vaccine is safe and effective.
Manufacturers must submit extensive data on the manufacturing process and the quality of the final product to regulatory authorities for review and approval.
The regulatory authorities may also conduct inspections of manufacturing facilities to ensure that they comply with good manufacturing practices (GMP) and other relevant standards.
Role of Cleanrooms in Vaccine Manufacturing
Cleanrooms play a critical role in vaccine manufacturing by providing a controlled environment that minimizes contamination risk and ensures high-quality vaccine production.
Cleanrooms are specially designed and constructed to maintain a high level of cleanliness by controlling the level of particles, microorganisms, and other contaminants in the air and surfaces.
Market Research Future’s latest report reveals that the worldwide cleanroom technology market is projected to expand from $4.7 billion in 2021 to $6.9 billion by 2030, with a compound annual growth rate (CAGR) of 4.9%.
This growth can be attributed to the escalating demand for cleanroom technology across industries such as biotechnology and pharmaceuticals, driven by an increased focus on product quality and adherence to regulatory standards.
In vaccine manufacturing, cleanrooms are critical in preventing the introduction of contaminants during the manufacturing process.
Using high-efficiency particulate air (HEPA) filters in cleanrooms can effectively remove particles and microorganisms from the air, minimizing the risk of contamination.
Understanding the GMP and cGMP Standards in Vaccine Manufacturing (KW here)
In vaccine manufacturing, adherence to Good Manufacturing Practices (GMP) and current Good Manufacturing Practices (cGMP) is essential to ensure vaccine safety, efficacy, and quality.
GMP refers to guidelines and standards that ensure products are consistently produced and controlled according to quality standards. cGMP, conversely, refers to the current GMP standards that regulatory agencies regularly update to reflect the latest advances in science and technology.
In vaccine manufacturing, compliance with cGMP standards is mandatory to obtain regulatory approval for vaccine production and distribution.
These standards cover all aspects of vaccine manufacturing, from raw materials to final product testing, and require manufacturers to establish and follow detailed procedures for every process step.
American Cleanroom Systems highlights the new manufacturing standards that differentiate GMP vs. cGMP, including continuous particle counting, digital temperature and room pressure alarms, digital storage of data, and hands-free bootie systems to maintain cleanliness in vaccine manufacturing facilities.
These additions to manufacturing standards help to ensure the highest level of cleanliness and quality control in vaccine manufacturing facilities, thereby ensuring the production of safe and effective vaccines for public use.
To learn more about the differences between GMP and cGMP standards in vaccine manufacturing, you can explore the American Cleanroom Systems website for detailed information on regulatory compliance in cleanroom environments.
Quality Control in Vaccine Manufacturing
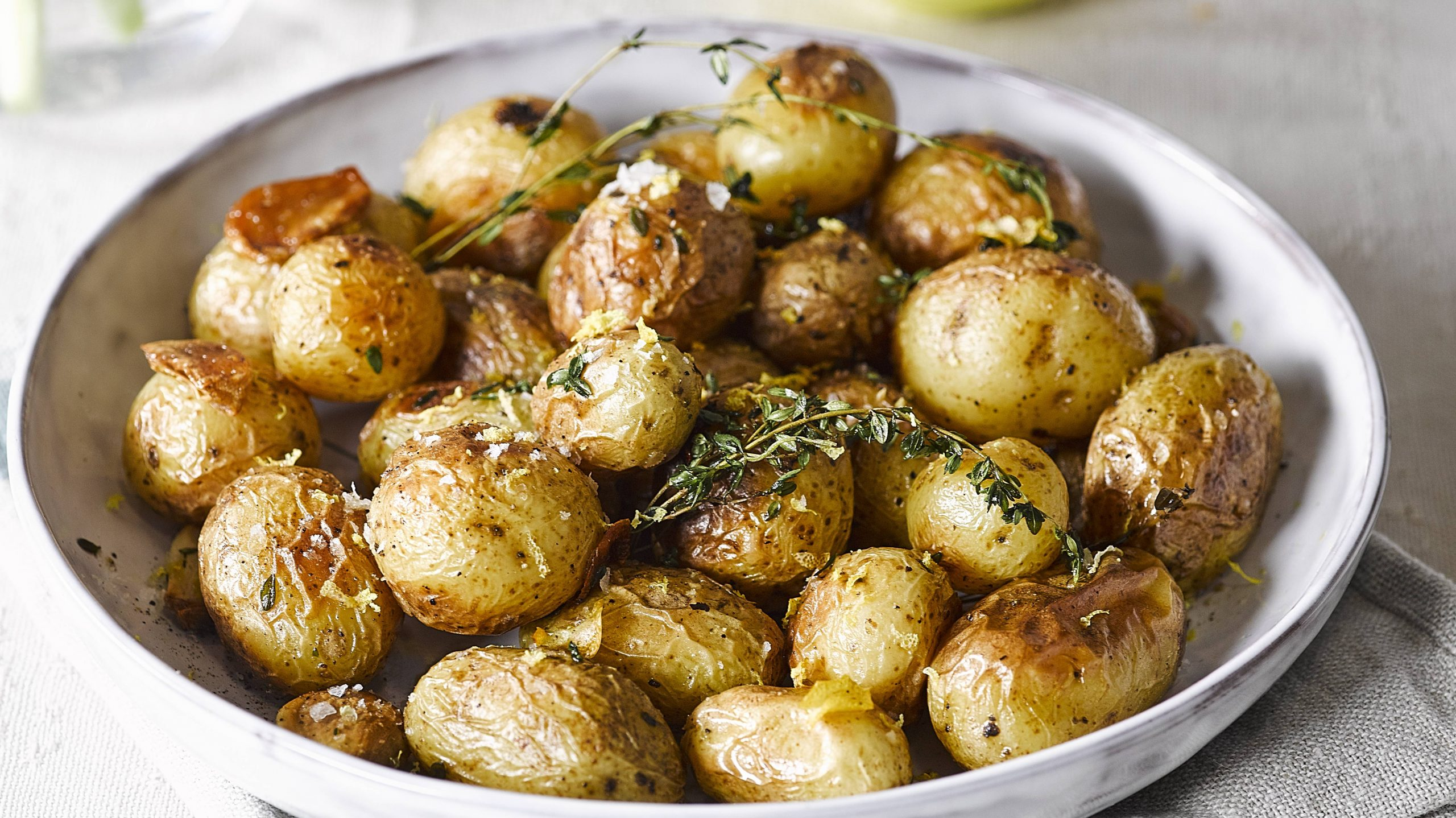
Quality control is crucial to vaccine manufacturing, ensuring that vaccines are safe and effective. For example, the Business Standard reports that more than 100 million Covid-19 doses got wasted in India, which amounts to $3 million.
This data highlights the importance of rigorous quality control measures in vaccine manufacturing to minimize waste and ensure the availability of effective vaccines for the population.
Quality control is critical to ensuring vaccine safety, efficacy, and availability, and recent data on vaccine wastage have further emphasized its significance due to poor quality control measures.
The quality control process in vaccine manufacturing involves testing for the vaccine’s purity, potency, safety, and consistency.
In addition, manufacturers must follow strict procedures for documentation and record-keeping to maintain traceability and accountability for each batch of vaccine produced.
Challenges and Trends in Regulatory Aspects of Vaccine Manufacturing
The regulatory landscape for vaccine manufacturing is constantly evolving, with emerging challenges and trends that require close attention from manufacturers and regulators.
One significant challenge is the increasing demand for vaccines due to the COVID-19 pandemic, which has led to a need for accelerated vaccine development and production while maintaining high-quality standards.
Another challenge is the complexity of vaccine manufacturing processes, which require advanced technology, specialized equipment, and skilled personnel.
This complexity can lead to delays in the production and distribution of vaccines, particularly in low-income countries.
One trend in regulatory aspects of vaccine manufacturing is the increasing use of advanced analytical techniques, such as genomics and proteomics, to develop more effective vaccines.
Another trend is the growing importance of global regulatory harmonization to ensure that vaccines meet consistent standards across different regions and countries.
The Role of Technology in Vaccine Manufacturing
Technology plays a crucial role in vaccine manufacturing, enabling the development and production of safe, effective, and readily available vaccines.
Advanced technologies, such as cell culture, recombinant DNA, and mRNA technology, have revolutionized vaccine manufacturing. It allows the production of more effective vaccines with fewer side effects.
Furthermore, technology has enabled the development of new vaccine formulations, such as combination vaccines that protect against multiple diseases.
For example, according to IFPMA, technology facilitates the production of vaccines in large quantities and tackles new variants allowing for rapid responses to disease outbreaks and pandemics.
However, the use of technology in vaccine manufacturing also presents challenges, like the need for specialized equipment and personnel and the risk of contamination during the manufacturing process.
To Wrap it Up
The regulatory landscape for vaccine manufacturing and quality control is not static, as it is subject to constant changes and updates in response to emerging challenges and trends.
Therefore, it requires continued attention and collaboration among manufacturers, regulators, and public health agencies to ensure vaccine safety, efficacy, and availability.
Overall, adherence to regulatory standards, robust quality control measures, and the continued application of advanced technologies are essential for the development of vaccines.
By adhering to the regulatory standards, you can ensure the production of safe and effective vaccines, which are critical to public health and disease control efforts worldwide.

Jean Smith is a fitness enthusiast and blogger who focuses on fitness and a healthy lifestyle. She is passionate about assisting people in living healthier lifestyles and is constantly on the lookout for new and creative methods to stay fit and healthy. Her articles are excellent resources for anyone interested in improving their health and fitness.